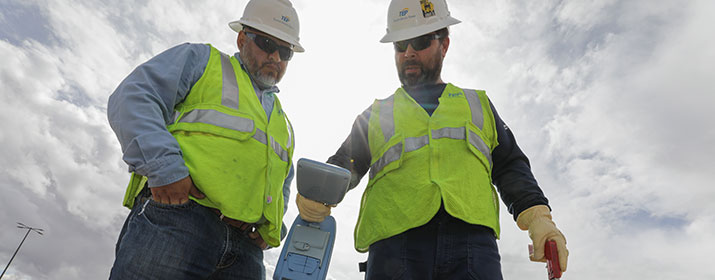
In southeast New Mexico, 62 wind turbines stretch across the remote desert landscape, generating clean, renewable energy. Working in such an isolated area can present unique challenges for the small crew of Oso Grande’s “caretakers.”
The Oso Grand Wind farm is TEP’s single largest renewable resource. It can generate up to 250 megawatts of power and produces enough power each year to serve the annual electric needs of 100,000 homes.
The wind farm itself spans 24,000 acres; that’s roughly 20,000 football fields, or the size of Florida’s Walt Disney World Resort. The closest city is Roswell, about 65 miles away. Reaching the system takes a full day’s drive from Tucson.
That means the team on site must have backup plans at the ready when replacement parts, equipment or specialized services aren’t available for our turbines, substation or lines.
When the team learned last year that an underground cable required maintenance, the Oso Grande staff needed to get creative. Under state law, they needed to have the line’s location marked before digging.
The problem was that Oso Grande staff didn’t have the capability to perform line location. Moreover, since TEP shares the leased land with others, the Oso Grande team would be responsible for responding to line marking requests from other land users in addition to serving their own on-site needs.
“We quickly recognized that line locating services would be needed to support our needs as well those of the local landowners and gas and oil companies whose lines may be located inside our facility boundaries,” said TEP’s Michael Bryan, Asset Manager for Oso Grande.
Several options were considered, included calling in help from the TEP line locating staff in Tucson and possibly using a contractor, but neither was feasible.
“Our line locators in Tucson are a nine-hour drive away and already have a heavy workload. By law, we also need to mark the lines within 48 hours of the request,” Bryan said. “We researched using local vendors, but the cost was too high and too variable and that runs counter to our focus on keeping rates as low as possible. We had no idea how many tickets we might get since this was our first year, and we needed a cost-effective solution to keep overall costs down.”
After brainstorming ideas with Transmission & Distribution leadership, the team decided to train Oso Grande wind technicians on how to locate lines. After procuring the proper equipment, the team brought in a vendor to provide training. The technicians also received hands-on training with TEP’s Tucson line locators with additional training scheduled for this year in Tucson.
“This was the best option for us and our customers. Training the Oso Grande staff just made good business sense and it gave them new skills. We were able to reduce costs while meeting the needs of our remote site,” Bryan said. “I’m sure other unexpected items will come up at Oso Grande in the future, but I’m confident we’ll bring innovative approaches to those challenges as well.”