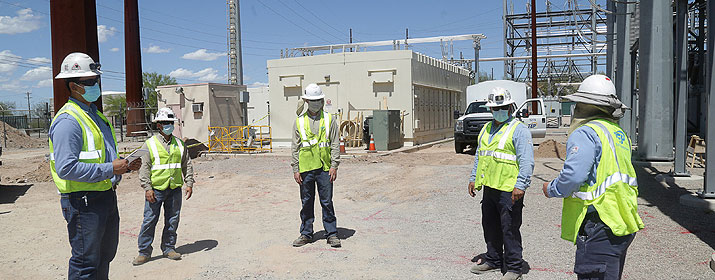
As a provider of a critical service at a critical time, Tucson Electric Power has remained vigilant during the coronavirus pandemic.
We adapted our work methods to protect our employees and the communities we serve while preparing our local energy grid for soaring temperatures and increased summer energy demands.
System improvement projects were prioritized to ensure the most critical were completed in time to serve customers during hot summer weather.
For example, TEP is nearing completion of the approximately $25 million Irvington to Kino 138 Kilovolt (kV) Transmission Line Project, which includes construction of a new 4.5-mile 138-kV transmission line and new 138-kV substation located at South Kino Parkway and East 36th Street. The new substation will include two new transformers, new circuit breakers, switchgear and capacitor banks. The new facilities will strengthen electric reliability for customers and meet growing energy needs in the area.
In midtown Tucson, TEP has nearly completed a $7.5 million upgrade of the Country Club Substation, where two transformers were replaced and new components were installed. Several related distribution line upgrades were completed over the last 18 months.
TEP also recently completed installation of a new 138 kilovolt (kV) transformer and switchgear at the Los Reales Substation in southeast Tucson, and installed 28 new 46 kV power poles to strengthen circuits interconnected through the North Loop Substation on Tucson’s north side.
This year’s summer preparations also included planning for possible COVID-19 impacts. TEP is ready to operate our local energy grid with a reduced workforce, if necessary, and we’re working with our neighboring utilities and reliability authorities to ensure reliable grid operations.
“We’ve worked very hard to continue providing great service to our customers while protecting our employees and the public by limiting the risk of disease transmission,” said Susan Gray, President and Chief Operating Officer. “We’ve had to get creative, coming up with new ways of being productive while staying safe and ensuring we’re well-positioned as we approach summer.”
To limit unnecessary risks of exposure, employees are now wearing face coverings, following social distancing guidelines, cleaning tools and equipment regularly, and limiting vehicle sharing. Crews are split into smaller teams, work schedules are more varied and daily safety briefings are held in more locations with smaller groups than usual.
At power plants in Tucson and Springerville, employees developed a skills and qualifications matrix to determine who could step in and perform the work of ill or quarantined colleagues. Employees now use different break rooms, hold pre-work safety meetings in large spaces, and even eat at different times to limit the potential for exposure.
Members of TEP’s System Control and Reliability team, which monitors and manages our local energy grid 24/7, also adopted alternate work practices. Shift change ‘handoffs’ are no longer face-to-face interactions. After one operator leaves a work area, another enters. Outgoing operators clean every work surface before they leave. The incoming operator does the same. Information that must be shared is passed along over the phone. The team’s daily work, however, hasn’t changed. They still interact with field employees over radio networks or on the phone, managing construction projects and system operation.
The adaptations – not to mention the continuing to commitment to customers – is not limited to critical employees. The company assigned more than half of its employees to work from home, including some members of TEP’s Customer Care team. Accommodating the change required significant effort from the company’s Customer Care and Information Services (IS) teams, since most service representatives had no laptops or remote headsets.
Even TEP’s Energy Programs team – which is most often found distributing shade trees, lightbulbs and energy kits at large community events –has refocused to highlight rebates and discounts that help customers save money right away.
“We know that people have lost their jobs and money is tight,” said Francisco Castro, Manager of Energy Programs. “However, those who do need to replace a broken water heater or air conditioning (AC) system should be aware of our incentives to reduce their out-of-pocket costs.”
Claims for residential AC rebates through TEP’s Efficient Home Program have actually increased, Castro said. “Customers with old AC units are being proactive. They’re looking ahead to the hot summer months and wanting to replace theirs.”